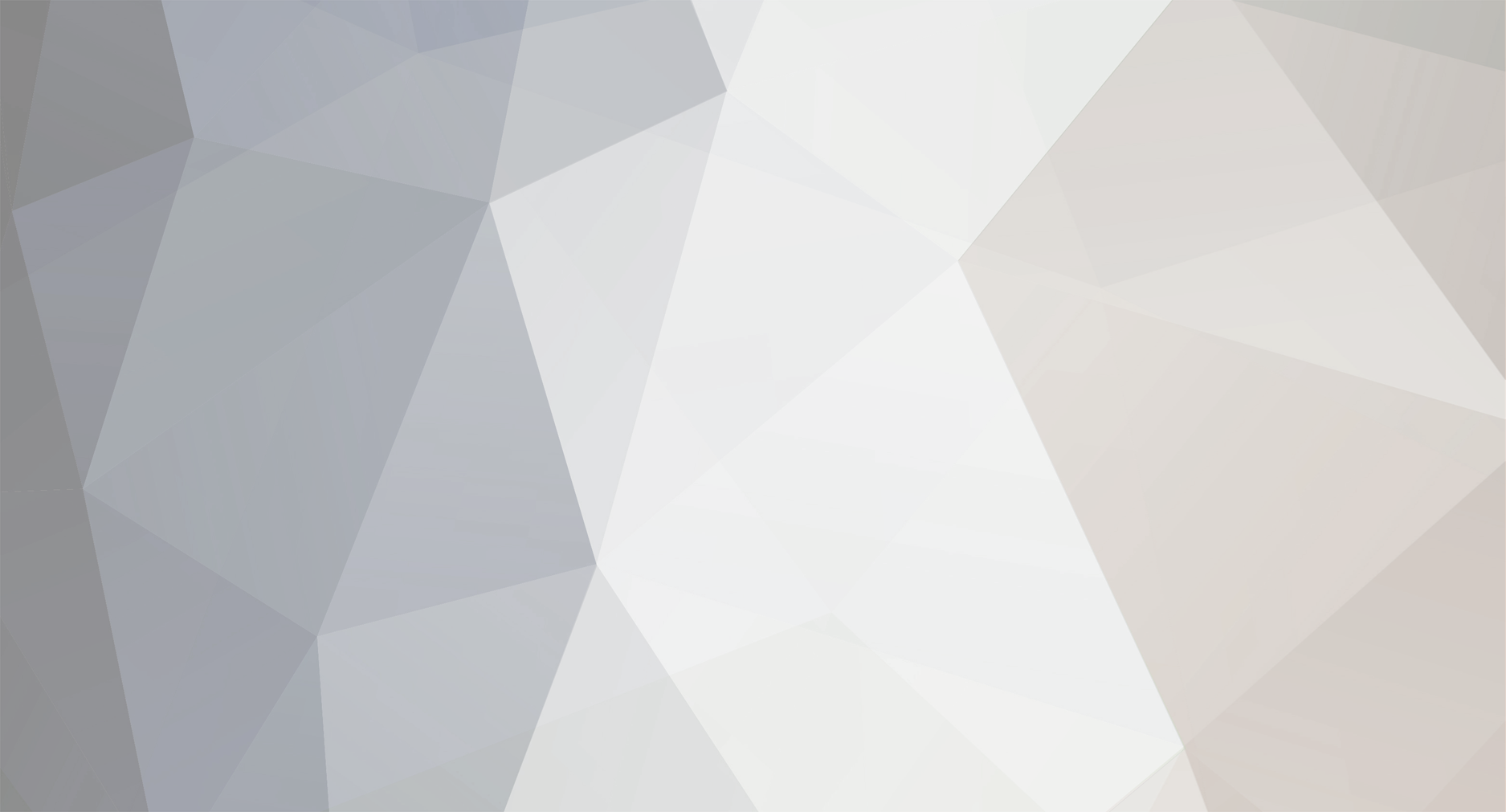
mike wilson
Members-
Posts
1,305 -
Joined
-
Last visited
Content Type
Profiles
Forums
Events
Gallery
Community Map
Everything posted by mike wilson
-
It's only depreciating in the US. Here we deprecate. Unusual for us to use fewer letters....... 8-)) One's man is too busy sorting out the exploding clutch, rattling valves and wonky electrics on one's Italian masterpiece to go snuffling about on the beach. Serves one's man right.
-
Round about nowhere*
mike wilson replied to belfastguzzi's topic in Special place for banter and conversation
The Griso's visible from _satellite_? -
More like learning to love your haemorroids.
-
Good article here: http://www.newmantools.com/machines/drillpoint.html If you go down to diagram "N" you can see what I mean about backing off the cutting edge. Bring the point (in cross section) of the edge back until you have something that makes more of a planing action than a cutting one. A fine whetstone run parallel to the longitudinal axis of the bit will work nicely in a couple of strokes. HTH.
-
I think you may have inadvertently posted to the wrong board. Whereas here there may be one or two here who occasionally get the wrong end of the stick, there are other boards where the majority get the wrong stick. p.s. Edison was a thieving, lying git.
-
Round about nowhere*
mike wilson replied to belfastguzzi's topic in Special place for banter and conversation
Thank you, thank you. It was the "cultural" part of desert that gave me the answer. 8-))) -
To describe it simply, you want a bit that ends up looking similar to a masonry drill. The cutting faces of a normal twist drill need to be ground back with a whetstone so that they are less of a sharp point. It's one of those things that is very difficult to put into words and indescribably easy to show someone. I'll see if I can find a website with the information in diagram form. Once the bit is properly formed, it will be much easier than farting about with hot needles. Not to mention safer.
-
Geoff's talking about 40mp (imperial) gallon. More like 30-35 to the US. About the same as you.
-
Don't forget to back off your drill bit's cutting edge before drilling the holes for fixing. Nowt more infuriating than a drill grabbing the workpiece. Well, there is - but it's still pretty annoying at the time.
-
Definitely. Note the statement on the same page about it "setting" quicker than other thermoplastics, too. Despite its lower strength, I think I would prefer acrylic for home working. Isn't polycarbonate also more susceptible to scratching? Good luck (may you acquire the requisite skills with the minimum of mistakes) anyway.
-
I meant the original assembler, in the factory. Not at all bored.
-
Especially if we can get both bike on the road at the same time 8-))) I'm just behind the southbound services at Washington.
-
Probably something as simple as the assembler having a dirty finger when they wiped installation lube on the bore. "Excuse me a moment please, my ear is full of milk" Oliver Hardy
-
I agree with your general principles but there are some "dark side" forces at work here. Airflow in induction and exhaust tracts was one of the arcane arts that people either had a feeling for or lucked into the right figures, until computer modelling came to the rescue. Even then, it's not cut and dried. To me, the two main things are to (i) make sure that the the samples are taken at the same timing of the induction on each cylinder. For that, you are going to have to use some sort of revolution sensor. There is already at least one in existence on EFI engines but you may not be able to use it for electronic reasons or reasons below. And (ii) on each cylinder, the samples need to be taken at a time that makes sense aerodynamically. No good sensing when the air is stationary, or nearly so. Which it is quite often. Ideally, the sensing should be done at peak air speed. That will vary through the intake cycle and at the specific location of the sensor. The existing bleed holes work fine for analogue comparative devices. There is no guarantee that they will do the same for a sampling device. You may have to take the samples there at timings that appear at odds with what you think should be going on in the inlet tract. To do that you may need to create a new timing sensor, which has to be properly attached and timed to the engine. Or you may have to place the sensor somewhere else. A thought on the sensor - you might be able to use one that senses high flow (using whatever parameter) and only takes measurements at that time.
-
I've got the GuzzitechDK DVD. I'll see if there's one on there tonight.
-
From the description of the wear/damage, I suspect that something like this has been the original problem. It's odd that only two bores out of four were affected, though.
-
Round about nowhere*
mike wilson replied to belfastguzzi's topic in Special place for banter and conversation
Must be Bungendore. -
I am not sure "vibration at idle and off-idle conditions" is correct. Balancing involves working at both tickover and throttle open conditions. Just because one is perfect does not mean that the other is. If you have perfect tickover synchronisation but a broken linkage between carbs/injectors, you will get very poor running off idle, to say the least. Whilst the rider perception of roughness may be more acute at tickover, it is also possible that poor synchronisation at open throttle settings is causing equal or greater problems due to the higher power being developed. Maybe this is one of those areas where people with two degrees in maths might care to take a few weeks to come up with a theorem, whilst the rest of us enjoy ourselves? 8-)
-
I really haven't a clue 8-) The pressure variations in that sequence will be huge. Digital sampling may not be the best option. But I am sure that, if you are sampling both cylinders at the same times, there will be a differential (or there is _likely_ to be a differential) due to the cylinder timings being offset. This will give you a false reading. I believe analogue sampling with proper damping will cause less problems unless you can find some way of timing the sampling for each cylinder, so that they are being treated identically. Maybe you could sample and discard all samples except the one with the highest reading?
-
What do you mean by lifter? Cam follower? Rocker arm?
-
If you are taking multiple readings (over, say, 1/10 of a second?) there will be variation even with damping and, depending on where in the cycle the readings hit, the average may not be a meaningful figure and would almost certainly not marry up with numbers taken from the other cylinder at the same time. This (matching cylinder timings) seems to be the biggest problem, to me. Is there some way of continuous measurement of a highly damped output using the components you propose?
-
Round about nowhere*
mike wilson replied to belfastguzzi's topic in Special place for banter and conversation
Good to see you back, BFG. _Now_ maybe we'll have some serious discussion. Good start. -
Where to begin? Depending on your machine, it is entirely possible to have perfect balance at tickover, yet wildly imbalanced carbs once the throttles are opened. The mechanisms for setup are often entirely different. The perception of balance can be most obvious at tickover, because the engine is running so slowly and due to the particular Guzzi configuration but, just because humans don't notice it so much, it doesn't mean that unbalanced forces are not having major effects at other times. I am having to examine your thought that the pressure differential has a decreasing effect at increasing throttle openings. Will get back to you on that. WRT your constant monitor, I think the main problems will be in two areas. Firstly, the sensor. There are various types that either measure pressure directly or can be modified to give you a reading. As an example of the second, you could use a hot wire air flow sensor to give you a reading that can be measured against one in the other manifold to give you an idea of "balance". A bigger problem will come with the Guzzi engine configuration. The large, slow and irregularly spaced pulses (especially at tickover) of the Guzzi engine will almost certainly cause problems with factors like resonance of the sensors. That is why I thought you might be using an indirect measure of manifold pressure, like an airflow sensor, which can be more easily and accurately damped. None of the above is intended to put you off. I think the idea is excellent but it may take more effort to make work than you originally anticipated.
-
rainwindrainwindrainwindsunrainwind is not much of a change.....
-
What would you use as a sensor? Heated wire? I entirely disagree with your last statement. Why do you think so?